XploR™ S-Seal and XploR™ FS-Seals for High Pressure High Temperature Oil & Gas Environments
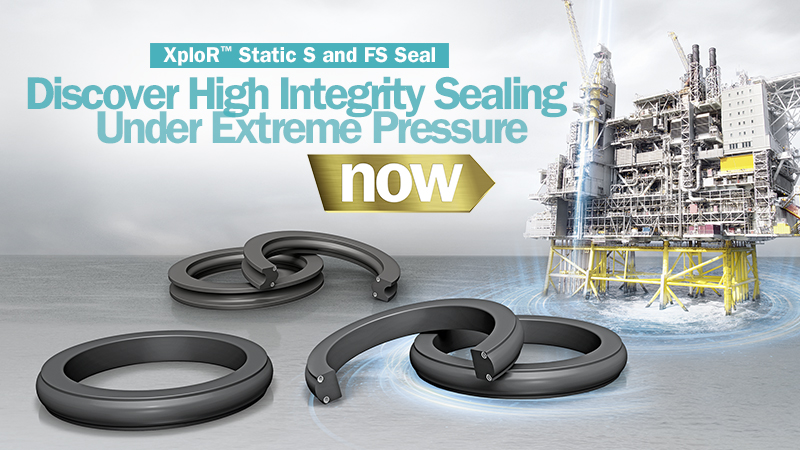
XploR™ S-Seal and XploR™ FS-Seal are custom-engineered, spring-energized elastomer seals. Meeting the needs of the oil, gas and energy industries, these offer maximum extrusion resistance in demanding high pressure, high temperature (HPHT) sealing environments.
James Simpson, Global Segment Director Oil & Gas and Energy at Trelleborg Sealing Solutions, says: “Our new XploR™ S-Seal and XploR™ FS-Seal combine the benefits of integral support components with the flexibility of an elastomer seal in static applications. Unlike typical O-Ring and Back-up ring or T-Seal solutions, these seals are single-piece components, engineered to make installation easier and safer. Being one component, the design removes the need for multiple Back-up Rings that require correct placement in the housing, significantly simplifying installation in closed grooves and in ‘blindly installed’ applications, reducing the likelihood of damage.”
>>Find out more about XploR™ S-Seal and FS-Seal
Specifically developed for the harshest conditions
The elastomer materials for the seals are from the XploR™ range of Trelleborg Sealing Solutions compounds specifically developed for the harshest of oil and gas processing conditions, providing resistance to Rapid Gas Decompression (RGD) and sour gas.
Molded into the elastomer profile of the XploR™ S-Seal and XploR™ FS-Seal, are two corrosion-resistant metallic anti-extrusion springs. These facilitate high pressure operation through a temperature range of -45 °C to +260 °C / -49 °F to +500 °F and ensure pressure transmits uniformly in all directions across the seal footprint. There is an option to overwind these springs with a Polyetheretherketone (PEEK) or carbon fiber composite material to meet specific pressure requirements.
Technical webinar
Join Global Segment Director Oil & Gas and Energy, James Simpson, for an in-depth look at the XploR S-Seal and XploR FS-Seal technology.
Key takeaways of the webinar include:
- Discover how the new XploR™ S and XploR™ FS-Seals can benefit you by simplifying installation and lowering total cost of ownership
- Understand how these seals improve the safety of critical systems in high pressure and temperature environments
- Learn how the flexible one-piece seal design optimizes sealing performance for leak-free applications
- Find out about our high-performance XploR™ materials, which are compliant to relevant global industry standards
Single piece design
The XploR™ S-Seal has a rectangular body and rounded seal surface. The seal replaces an O-Ring and Back-up Rings or T-Seal in HPHT static applications. The XploR™ FS-Seal profile has a concave feature on the base with a rounded sealing surface. This allows for increased compression in HPHT situations, specifically for large diameter clearance requirements.
Certifications and testing
Static test fixtures provided in-house testing of typical requirements for American Petroleum Institute (API) 6A PR2 certification. This testing validates the compatibility of the XploR™ S-Seal and XploR™ FS-Seal at specific pressures and temperatures as indicated by the test protocol. Materials are NORSOK and ISO 23936 compliant.
Learn more:
>>Download the XploR S-Seal and XploR FS-Seal flyer
>>Contact us to discuss your high pressure application
Press release:
>>Download the English press release
>>Download the press image